Home - Core values - How Hydrex helps shipowners save money
How Hydrex helps shipowners save money
Ships are large, complex pieces of equipment with many, many working parts that require maintenance and that can fail and need repair. Because they are at sea, often far from land or a port, there is a safety aspect to their proper maintenance and repair which is even more crucial than for land-based vehicles. The repair and maintenance involved can come at a very high cost.
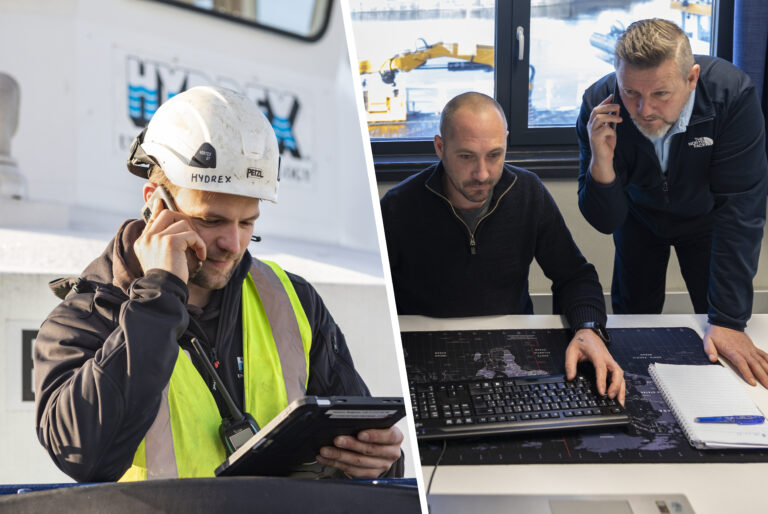
Anything that can reduce the cost of maintenance and repair while maintaining efficiency and safety and keeping the ship in business and on-schedule is therefore a valuable resource to shipowners and operators.
One of the benefits Hydrex offers to shipowners and operators all over the world is cost savings.
How do we do this?
The first step: to drydock or not to drydock?
Drydocking a ship under any circumstances is a very expensive exercise. There are two sides to the cost: there are the drydock fees and the cost of the maintenance or repair carried out in drydock; then there is the off-hire time while the ship is out of service. These both affect the bottom line equally.
Certain drydocking is mandatory, routine and scheduled. If an intervention is required when the ship is not due to go to drydock, the revenues lost as a result have a direct effect on the bottom line for the ship and its owners, just as much as the direct costs and fees involved.
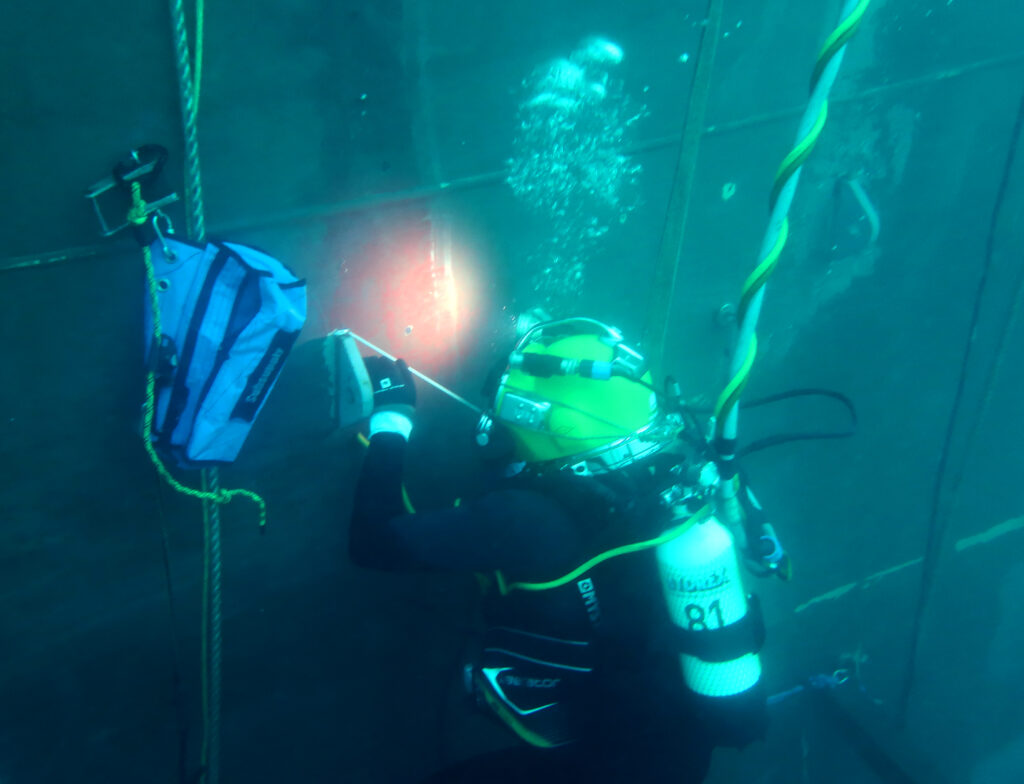
Nevertheless, these situations do arise, and not infrequently. The stern tube starts leaking oil and the ship is not approved to sail until it is repaired and the leak stopped. The ship grounds or touches something and the integrity of the hull is jeopardized, or the propeller blades are bent. Cracks develop. A thruster ceases to operate, making the ship impossible to maneuver properly so that tugs are required. The acids in the scrubber exhaust eat away the steel and the ship begins to leak. Rudder malfunctions, stabilizer problems, clogged seachest grids and a thousand other problems can develop which interrupt the ship’s scheduled itinerary and operations.
When any of these circumstances arise, the Captain, Chief Engineer, Superintendents and Ship Managers are faced with a difficult decision. Drydock the ship for repair? Or try to get the needed repair carried out as rapidly as possible with the ship still afloat?
This is where Hydrex can be a real asset to anyone responsible for keeping a ship in good repair and operating safely. They can simply call us, explain the situation they are faced with, and ask us if we can carry out the needed intervention without the ship having to go to drydock.
“Without charging anything for this service, we will determine from the information at hand or that we can obtain, whether the needed repair can be carried out with the ship afloat, or whether the ship has to go to drydock,” says Hydrex’s Founder and CEO, Boud Van Rompay. We will examine the situation, study any drawings, photos or videos provided, talk to the officers and engineers involved. “When we say, ‘Yes, we can do it with the ship afloat,’ or, ‘No, we think you will have to go to drydock,’ that represents the shipowner’s first cost saving with Hydrex. “That initial free service can represent a huge cost saving. “If we determine we cannot carry out the operation underwater with the ship afloat, you can be sure that nobody else is likely to be able to do it either, so the only choice is to go to drydock,” Boud continues. “But very often we will undertake in-water repairs that others cannot do, because they don’t have the personnel, organization, equipment, know-how, ingenuity or experience needed. In those cases, the shipowner will save large amounts of money by having Hydrex do the job.”
Either way, this initial decision is an important one in the overall saving of unnecessary costs.
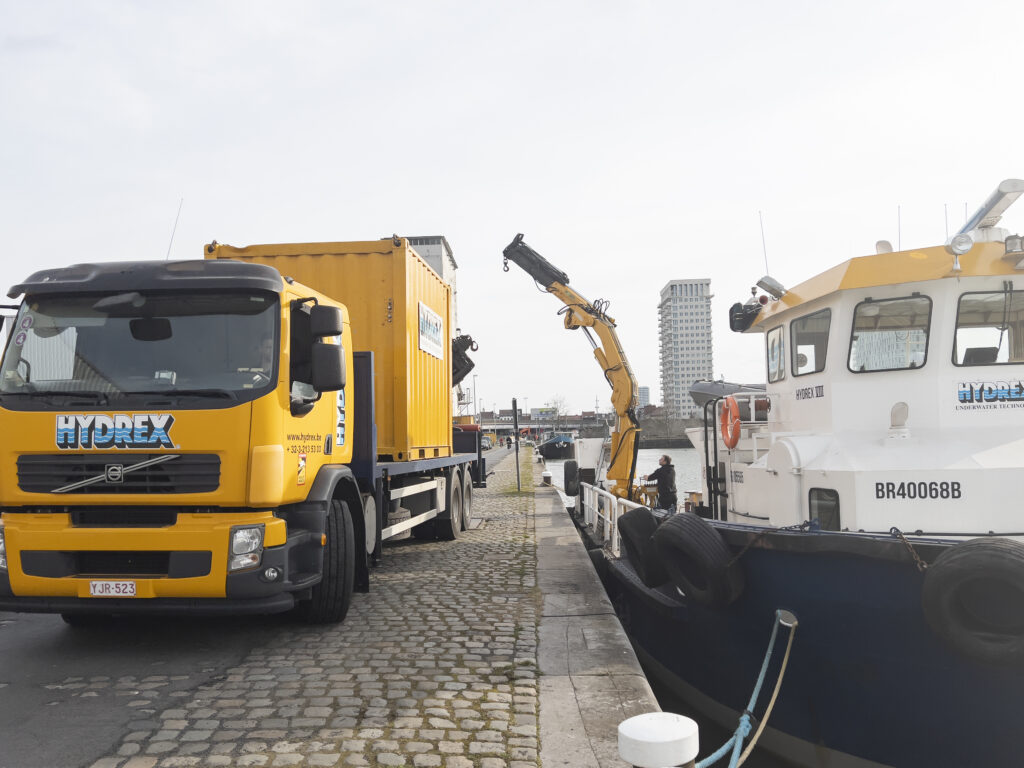
Accurate estimates
Once the decision has been made that the job can be successfully carried out without the need to drydock, the next step is an accurate estimation of the time and costs involved.
“We provide estimates based on the information we have about the situation we will be dealing with,” explains Dave Bleyenberg in Tech Services at Hydrex. “If this information is accurate, then we usually complete the job within the time and cost estimate we provide. This is not usual in this industry. We are able to do this because of the experience and knowledge of the key decision makers in the company and because we train our technical personnel on courses including practicing the procedures here at our headquarters so that when they are on a job they can perform as efficiently as possible.”
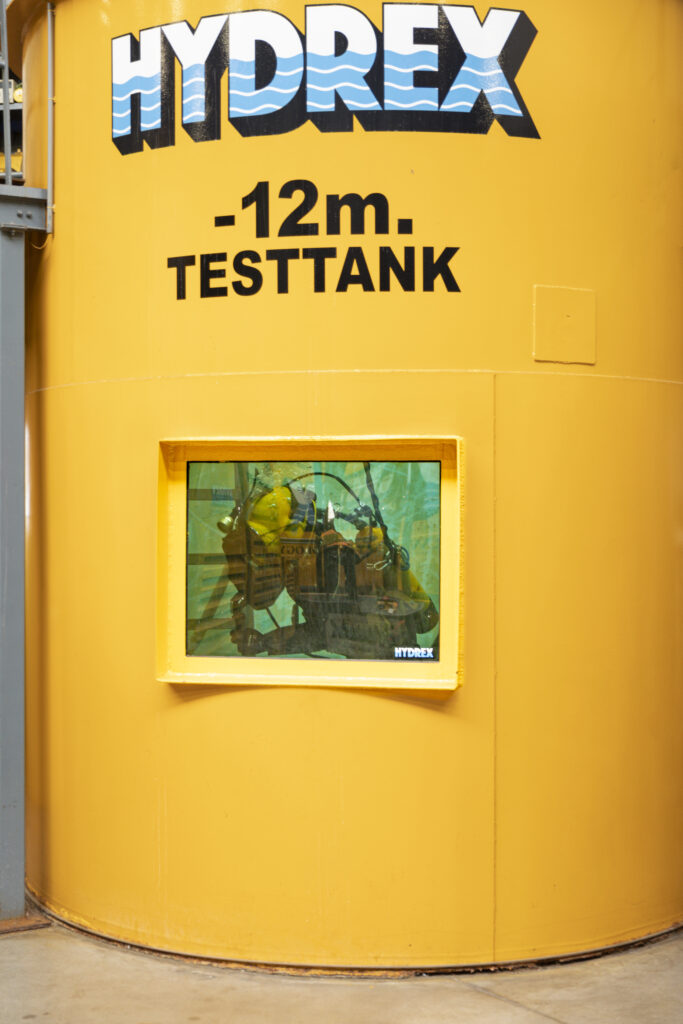
Speed, quality, reliability
Once we and the shipowner or manager have decided to go ahead with an in-water repair, the next major savings to be made are through the quality and speed of the operation. Just comparing hourly costs of various underwater service providers and choosing the cheapest does not guarantee cost savings. It is the final invoice and also quality of the repair and how long it will stay repaired that tell the tale. If a new insert is installed but it starts leaking again after a few months, no money has been saved.
Quality and reliability are essential if the repair is going to prove cost-effective overall.
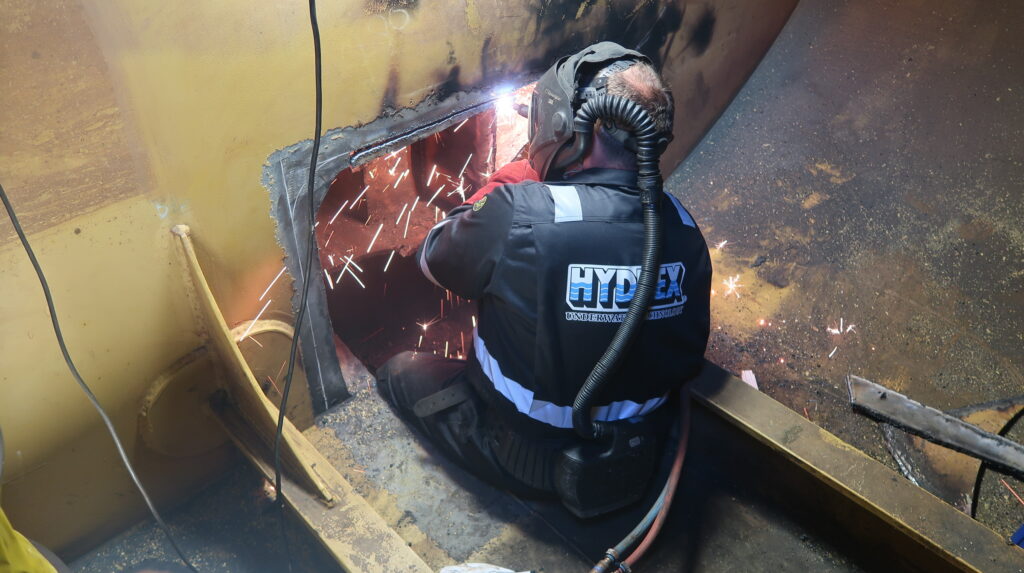
When it comes to speed of delivery, it is generally reckoned that there’s no comparison to Hydrex. “We get the job done dramatically faster, often cutting the time others would take in half or less,” says Boud. “Since the company was founded, we always took great pride in how quickly we could get the job done.”
Boud recalls, “We took a decision right at the start that we were going to get each job done to the highest quality standards and requirements, observing all safety precautions, as rapidly as the job could be done. It was based on a sense of giving value for money and also establishing our reputation and trust with the market. Our customers gained confidence that jobs could be done very quickly.”
The quality factor comes down to doing all the steps necessary to meet the standard or the class requirement for a particular job. “You don’t waver,” Boud explains. “You look at the steps that are needed and then you just do them, no matter how difficult. Some people cannot see the steps to take in order to get there because it is overwhelming. That’s where training comes in.”

Conclusion
The first cost saving is establishing whether or not the job can be done without going to drydock. This is a free service.
If it can be handled with the ship afloat, the next step is providing an accurate estimate. The next cost saving comes in doing the work as quickly as humanly possible to the highest quality standards while keeping safety firmly in mind.
Your ship is back in action without interfering with the charter, without loss of time, and interrupting the commercial activities as little as possible if at all.
If you have any questions regarding our underwater services, do not hesitate to contact us. We are at your disposal 24/7 and ready to mobilize almost immediately.
+32 3 213 53 00
hydrex@hydrex.be
News and projects

Complex steel repairs carried out afloat
Hydrex has an in-house Research & Development department that can take care of the engineering aspects of an operation. In
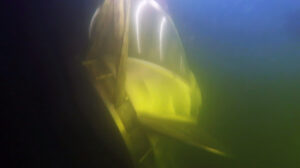
Start saving fuel with your propeller cone fin now
We regularly install propeller cone fins on different types of vessels. We can carry out these operations underwater, out of
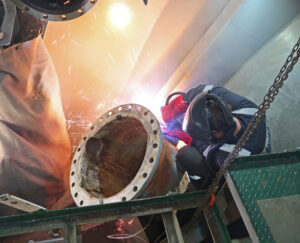
The solution to scrubber corrosion
More and more ships are being fitted with Exhaust Gas Cleaning Systems (EGCS or, more commonly, scrubbers) so that they