Recently our diver/technicians carried out scrubber overboard pipe repairs on two ships in Munkebo, Denmark. In total seven corroded pipes were repaired. On five pipes the corroded areas of the scrubber pipes were ground out and rewelded. The pipes were then protected with Ecospeed, a chemically resistant coating produced by Subsea Industries. The same protection was given to the two new pipes that were installed.
Exhaust scrubbers are systems that filter out the harmful noxious elements from the exhaust gases of marine diesel engines. These can severely corrode the pipes of the scrubber which can result in water ingress if not handled quickly enough.
Replacement and repairs
A 295-meter LNG carrier needed maintenance and repair work carried out at the Fayard shipyard in Munkebo, Denmark. We were asked to perform repairs on three scrubber overboard pipes while the ship was berthed at the yard.
One of our teams traveled to the vessel’s location. After arriving at the ship on one of yard’s workboats they first performed an inspection of the damaged areas on both the waterside and the onboard side of the hull.
This revealed that two of the pipes needed to be completely replaced. As the corrosion on the third scrubber overboard pipe was not yet severe, a full replacement was not needed.
Because of the location of the damaged parts of the pipes, welding work on the inside shell plating of the hull was needed. As a result, the outside of the overboards could not be sealed off with a simple patch. Custom cofferdams were designed and constructed at our workshop.
After the installation of the cofferdams, the team cut away the old pipes. The shell plating was then prepared for the installation of the replacement part. New pipes had also been constructed at our workshop in Antwerp. The pipes were then positioned and secured with a full penetration weld. Next an independent inspector carried out NDT testing of the welding work.
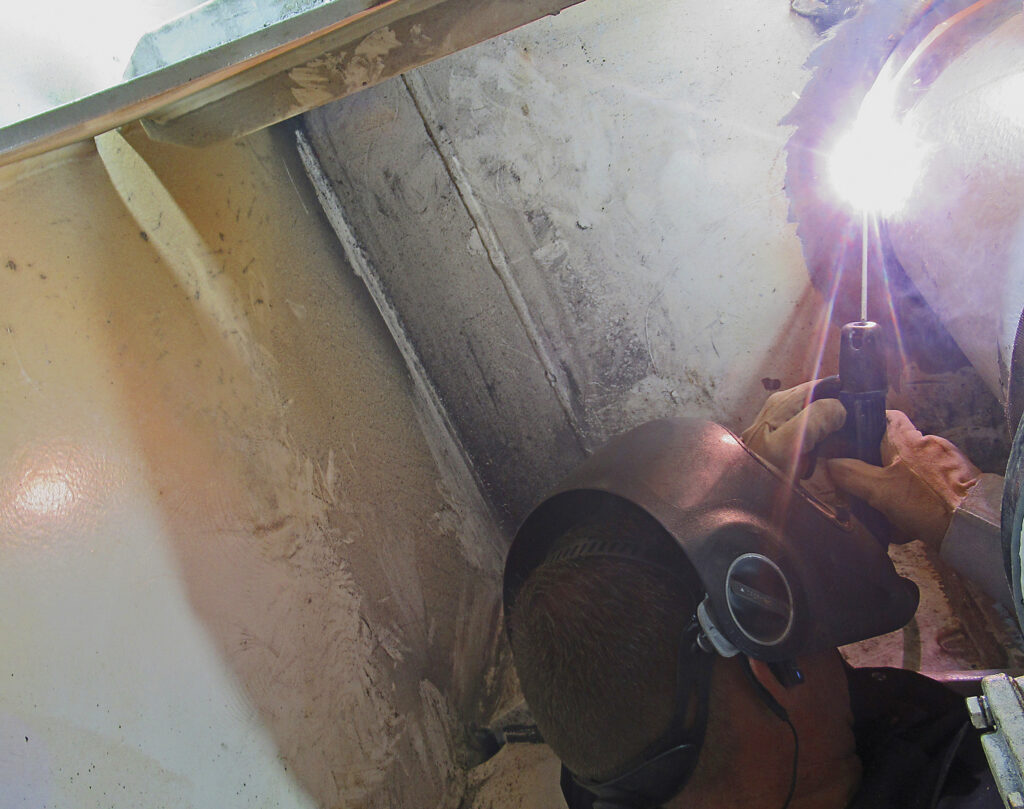
Our diver/welders then sealed off the outlet of the final overboard pipe. The team ground away the corroded area before rebuilding it back to its original thickness.
When the welding was complete the surface was cleaned and a Magnetic Particle Inspection (MPI) was carried out by an independent inspector.
Lasting corrosion protection
To prevent both the new and the repaired pipes from corroding, the inside was coated with Ecospeed. This product is produced by Hydrex’s sister company Subsea Industries. Ecospeed is highly chemically resistant. Considering the nature of the process taking place inside a scrubber, this is essential for lasting protection of the pipe. Ecospeed should also be used to protect a newly installed scrubber system from day one.
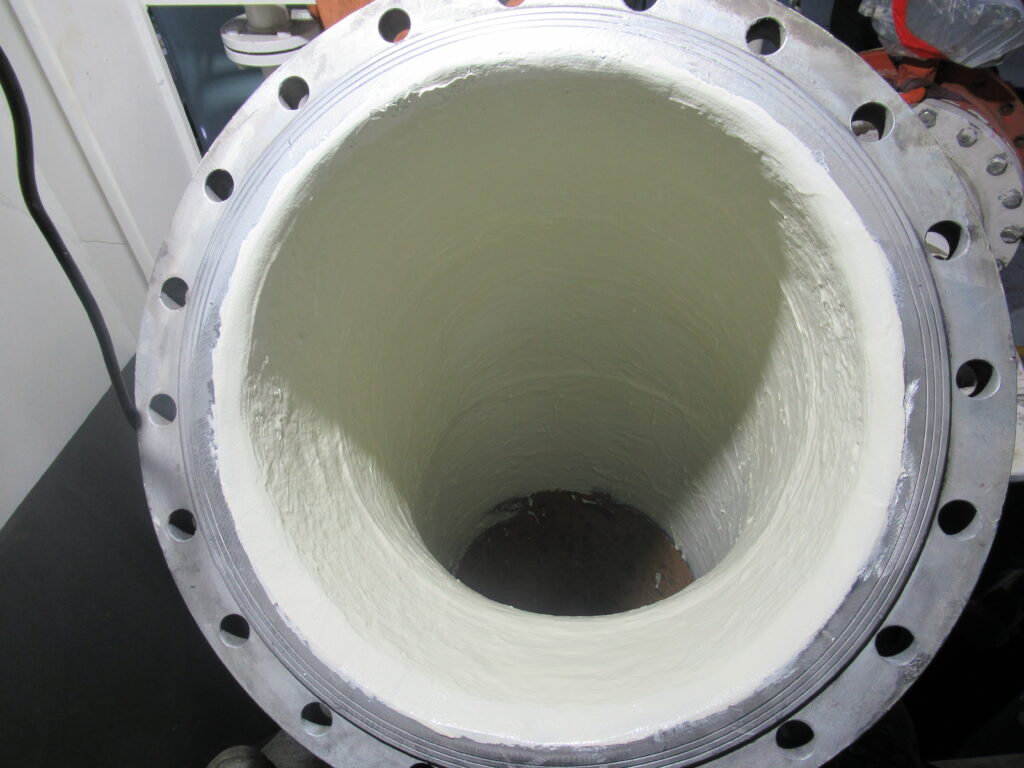
A month later the LNG ship’s sister vessel came to the yard and we were once again asked to perform an inspection and any needed repair of the scrubber overboard pipes.
Luckily the corrosion on the scrubber overboard pipes of this vessel was less severe. A full replacement of the four pipes was not needed.
Our diver/welders repaired the pipes using the same procedure as on the first ship. The inside of these pipes was also coated with Ecospeed to keep them safe from further corrosion.
Conclusion
We offer a full package to owners that are experiencing similar damage. We replace the corroded exhaust pipe while your vessel stays on schedule and we make sure that you will not have to call us again in a few months’ time with the same problem.
Most ships sail on a tight schedule. We know how important it is to prevent any loss of time. Our technical department has many years of experience in drawing up a repair plan that fits in perfectly with a vessel’s schedule. Working in shifts or splitting up an operation in stages are just a few of the many ways we can make sure that the impact of the repair is limited to the absolute minimum.
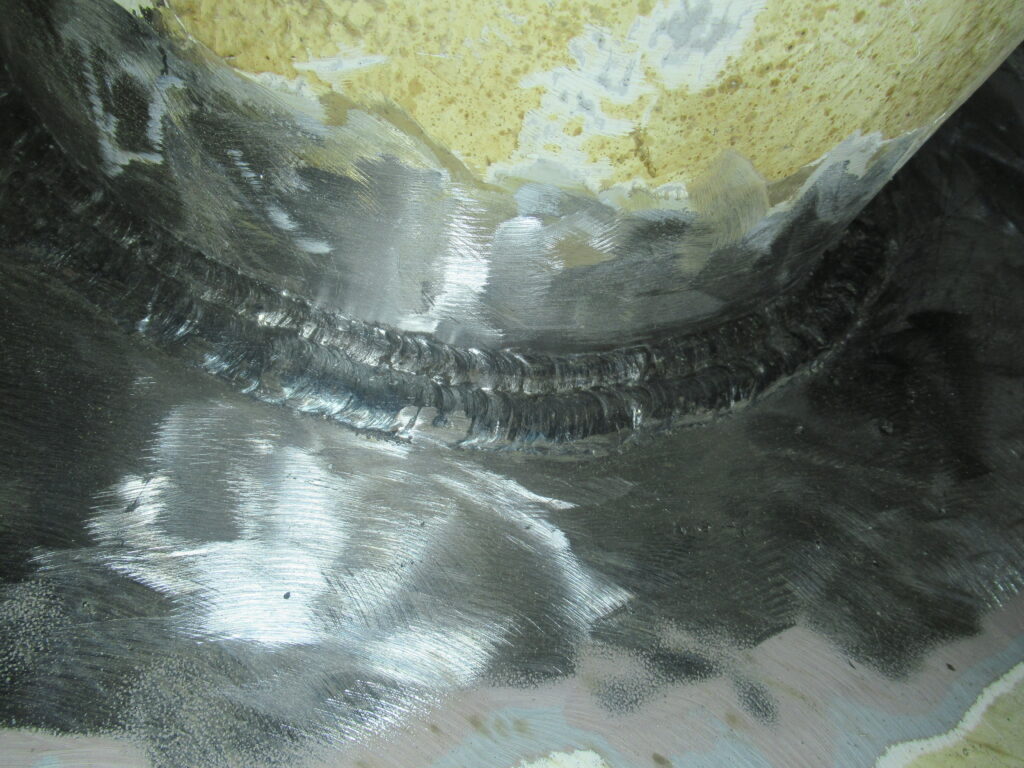
If you have any questions regarding a possible scrubber repair, do not hesitate to contact us. We are at your disposal 24/7 and ready to mobilize almost immediately.
+32 3 213 53 00
hydrex@hydrex.be
Click on the images below for more scrubber repairs and other case studies.
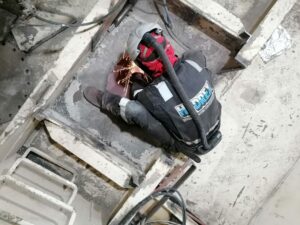
Scrubber overboard pipe repairs in Belgium, France, Spain and Malta
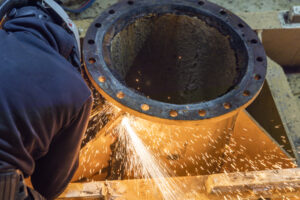
Scrubber overboard pipe repairs in Belgium and the Netherlands
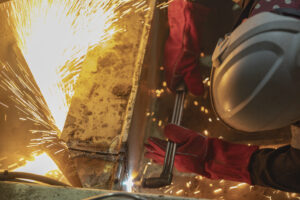
Routine scrubber overboard installation
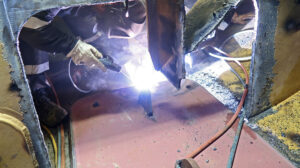
Permanent underwater insert repair on bulker in France
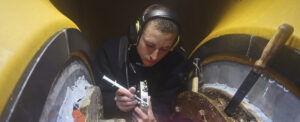
Double stern tube seal repair on second vessel in Tasmania confirms customer’s trust
