Our diver/technicians can perform a wide range of repair or maintenance work on bow thrusters. An entire unit can be overhauled, propeller blades and seals can be replaced or repair work on another specific part of a thruster can be performed on-site. These repairs are performed in cooperation with all OEMs and can be carried out while the ship stays afloat, with minimum impact on its schedule.
Our goal is to offer you the most efficient solution while maintaining the highest safety and quality standards. This article gives a few examples of the many bow thruster repairs carried out by our teams.
Underwater bow thruster reinstallation in Italy
A month after we removed the bow thruster of a 300-meter container ship our men once again mobilized to Italy. They reinstalled the overhauled unit underwater with the use of our flexible mobdock technique.
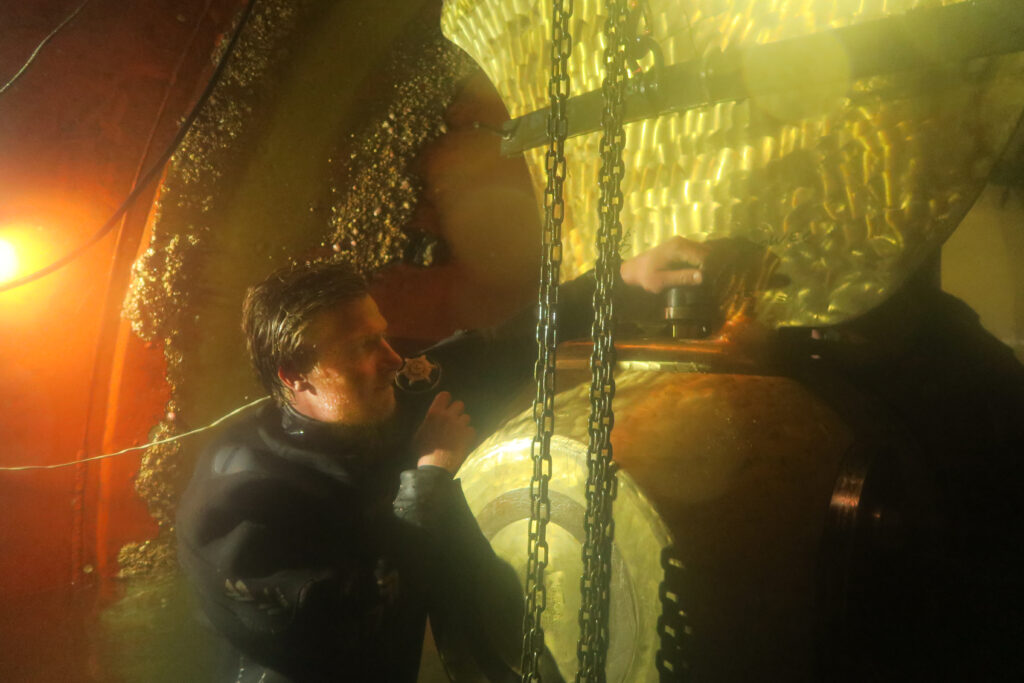
The available time window for the removal of the bow thruster had been very short because of the tight schedule of the vessel. For this reason, the job was split in parts, performed in different ports.
The time frame for the reinstallation was slightly larger, allowing our team to carry out the job during a single stop of the vessel. The divers maneuvered the overhauled bow thruster back into the thruster tunnel which was then closed off using our flexible mobdocks.
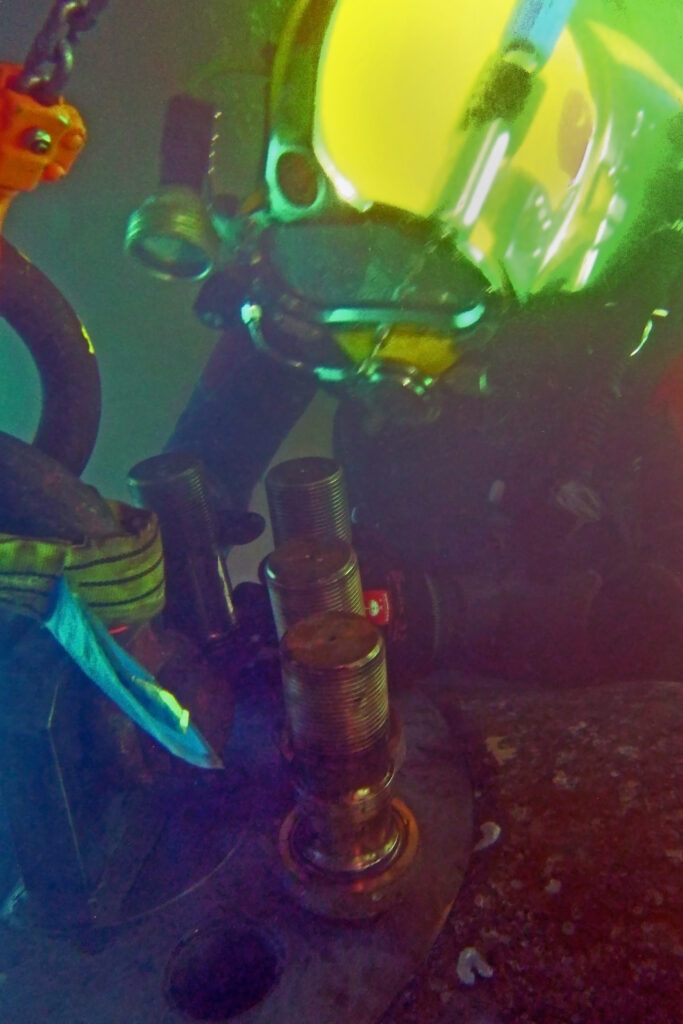
All water was pumped out of the tunnel. This created drydock-like conditions for our divers while the vessel stayed afloat. The team then secured the unit and connected it. Once this was done the thruster propeller blades were installed one by one. With these in position and the bow thruster tested to make sure if was functioning correctly, the ship was ready to sail.
Our teams worked in shifts around the clock to finish all tasks as fast as possible. As a result the charterer did not have to worry about his vessel’s schedule.
Thruster repair afloat in Phuket
A 200-meter cruise ship experienced a problem with its bow thruster A breakdown had occurred in the feedback system that specifies the position of the vessel’s bow thruster blades. Taking into account the strict schedule of the cruise ship, keeping it sailing was essential. We were contacted by the customer and asked to find a fast, on-site solution.
In cooperation with the manufacturer of the thruster, a plan was devised by our technical department. Our diver/technician team would carry out an inspection and any necessary repairs afloat without removing the unit from the thruster tunnel. The customer gladly accepted this proposal as it meant he did not need to take his ship into drydock.
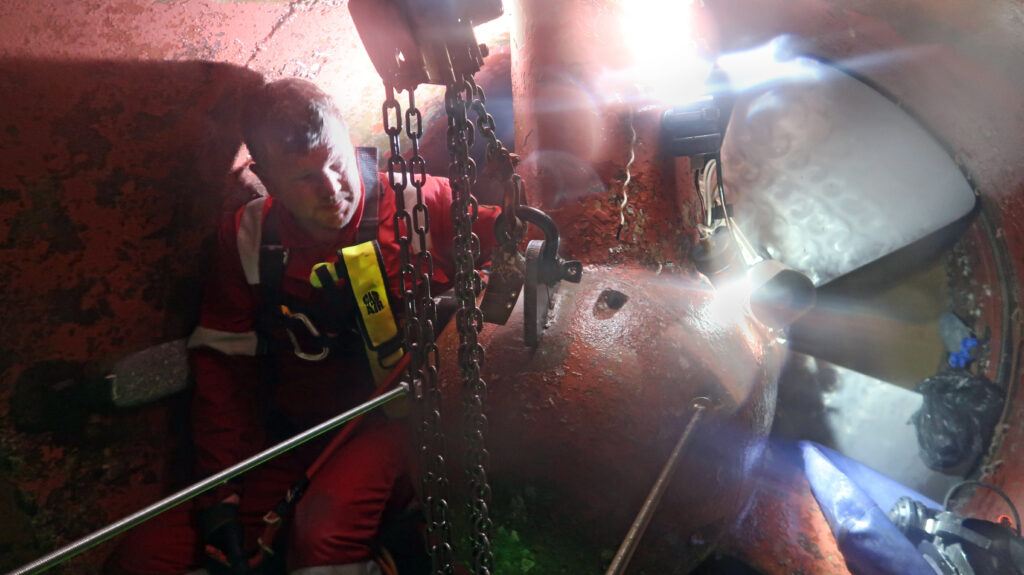
We therefore mobilized a team to Phuket, Thailand to perform the necessary underwater repairs with the use of our flexible mobdocks.
Our team had a very cordial and smooth cooperation with the crew of the ship, the manufacturer of the thruster and all other parties involved. This helped us to perform the operation as fast as possible, thus saving the owner considerable time and money.
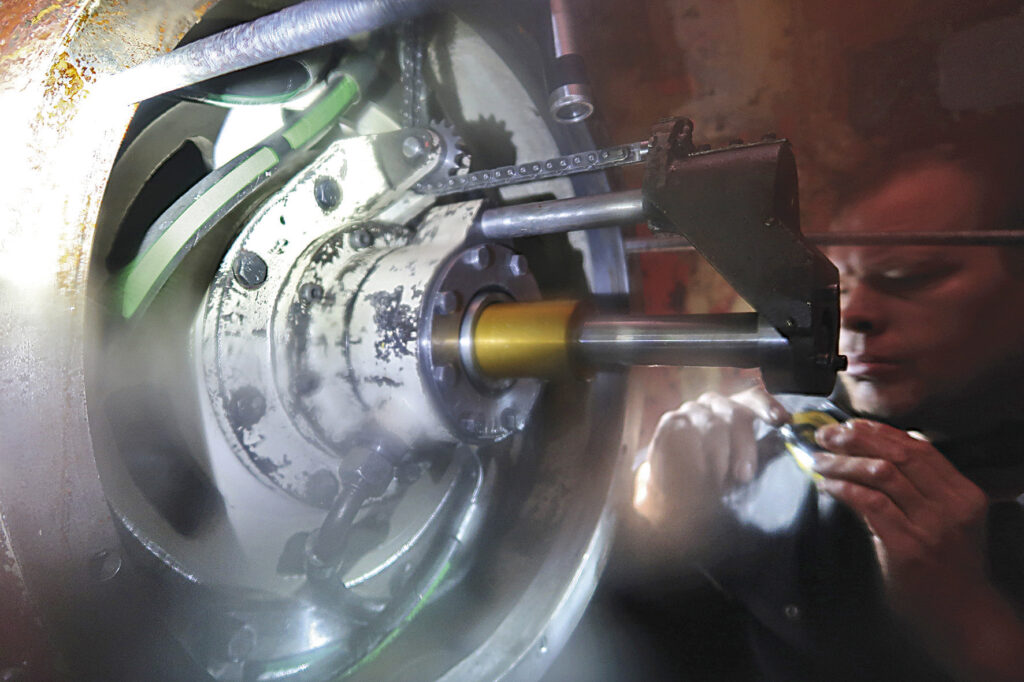
Underwater operation in stages avoids loss of income
A Hydrex diver/technician team removed a bow thruster unit which needed to be overhauled from a 363-meter container vessel in Rotterdam. Because of the ship’s tight schedule in that port, the time required to remove the thruster unit had to be reduced to the absolute minimum.
To help economize on time, the team had already prepared the thruster tunnel during the ship’s stop in Le Havre, France. This allowed the divers to perform the operation underwater in a very short time frame without interrupting the vessel’s schedule.
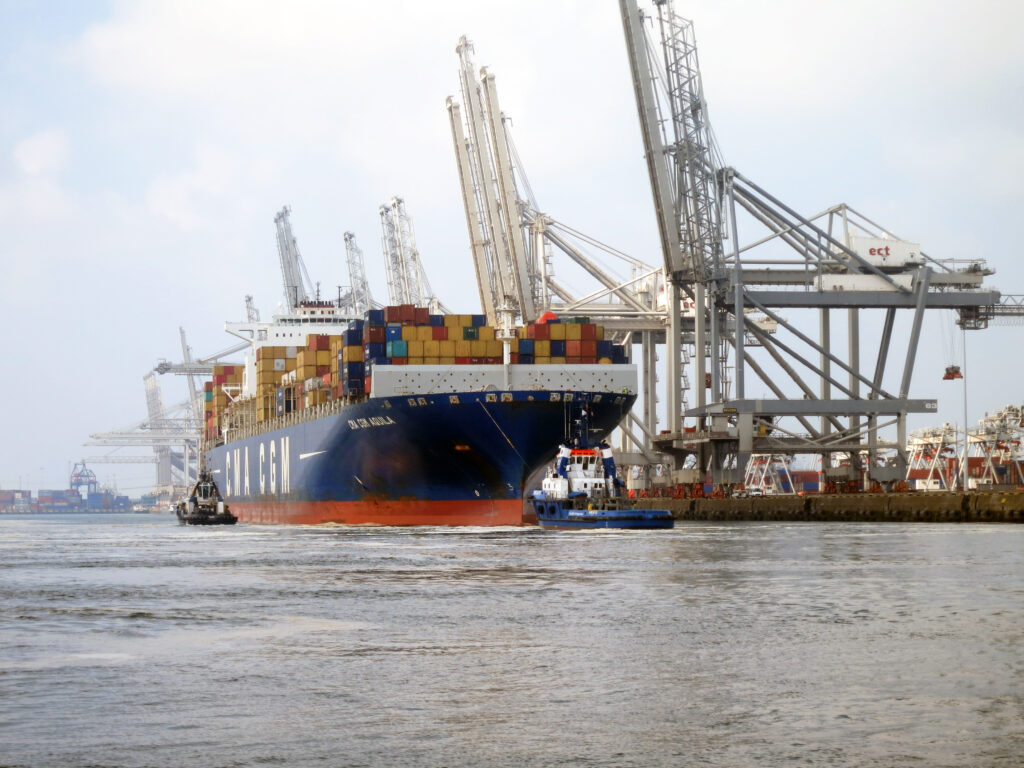
Off-hire time causes a substantial loss of money. It was therefore very important that the ship could keep its schedule. Performing the removal in two stages allowed this. This kind of flexibility can only be achieved successfully by staff who have familiarity with such operations and have the relevant knowledge and equipment. We have a technical department capable of executing all the required planning while our diver/technicians are trained and qualified to perform the full range of required, class-approved repair procedures in even the harshest conditions.
An animation of the procedure used can be found here.
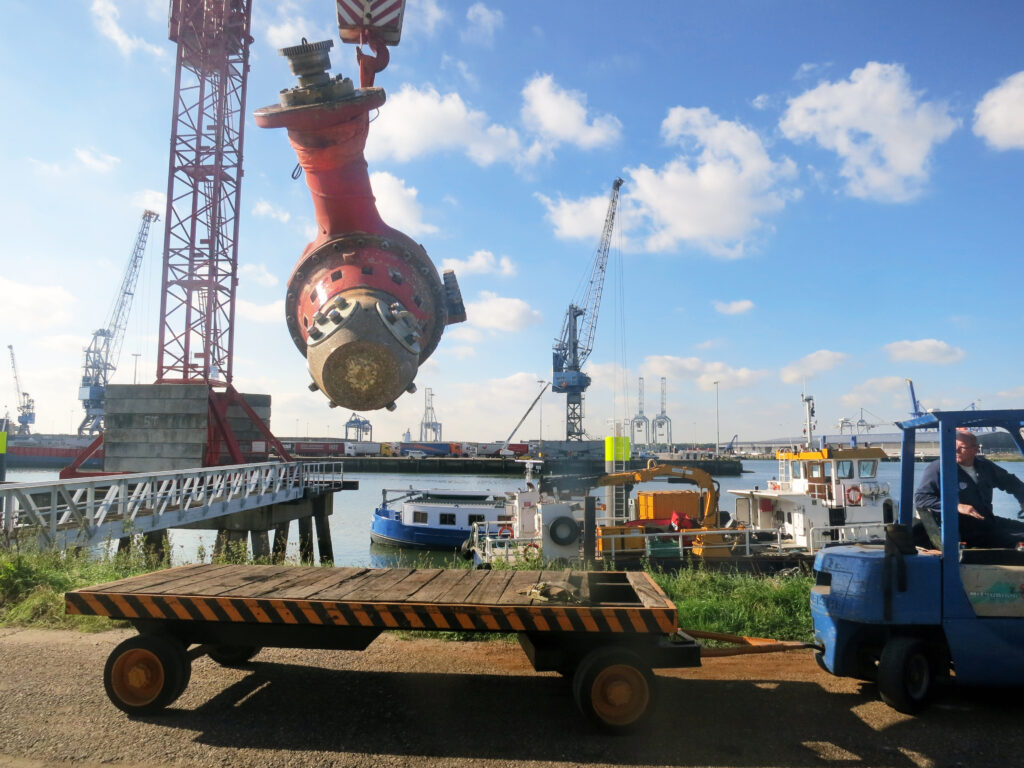
If ever you would encounter a similar situation, give us a call. We can then tell you if the repair is feasible and start working on its handling.
+32 3 213 53 00
hydrex@hydrex.be