Our teams regularly carry out cold straightenings, croppings and other propeller blade modifications.
Winter months usually result in an increase in propeller repairs. Throughout the rest of the year we also attended vessels for inspections of propeller blades that are broken or damaged by ice or debris
Returning bent blades to their original form
For instance, we sent a team to Taranto, Italy, to inspect a 27,500dwt general cargo ship. Its engineers had reported excessive vibration from its five blade, 5m diameter propeller as the vessel returned from operations. The cause of the vibration was two bent propeller blades.
We deployed our in-house developed cold straightening equipment and a dive team to repair the blades. This was done without disruption to cargo operations and the vessel’s ongoing schedule.
After correctly positioning the cold straightening press over the propeller blades, they were bent back into shape. While our divers were repairing the propeller underwater, the team leader ashore monitored video links from underwater cameras on the divers’ equipment. This allowed us to communicate the exact dimensions and position of the damage between the divers and the technical team supervising the operation. This is essential because the calculations need to be perfectly accurate to achieve the best results in terms of propulsion efficiency.
Cropping severely damaged blades
This operation involved the repair of bent propeller blades. If straightening however is not an option, the damaged area of the blade can be cropped and grinded to restore hydrodynamic balance.
This was done during an emergency operation on a tanker berthed in Antwerp. A doubler plate installed on the inside of the propeller nozzle had partially detached itself and had severely damaged the four blades. First a detailed underwater inspection was carried out by our divers to assess the extent of the damage and to calculate the ideal cutting line. The doubler plate was then removed to prevent it from causing further damage. Next the four blades were cut underwater, grinded and polished using our patented blade repair tool.
If five-bladed propellers are damaged, the repair is more complex as extensive calculations have to be made to take the right amount off each blade to restore balance and prevent vibration.
We often encounter blades that have been severely damaged, chipped or almost completely broken off during ice navigation. In most instances, they can still be repaired on-site by grinding and cropping the blades.
Wide range of propeller modifications
Luckily, the damage to the propeller blades is not always so extensive and a less comprehensive repair is required, as was the case for a 183-meter tanker in Tenerife.
An underwater inspection revealed that two of its propeller blades had suffered smaller cracks and dents along their trailing edges. Because the damage to the blades was limited, the ship experienced no vibrations and only a small loss of performance. Our divers therefore grinded away the cracks and polished the edges of the blades. This gave the propeller back its original efficiency and prevented further cracking.
Our teams can also provide prescriptive propeller maintenance. When a container ship suffered propeller damage after a particularly severe winter, the owner wanted to find a way of preventing ice-damage to propellers on other vessels in the fleet.
We strengthened the blades with modifications based on a specific design developed in cooperation with the original equipment manufacturer. The strengthening made them significantly less susceptible to ice-impact and debris, without decreasing the propellers’ performance.
Conclusion
Over45 years of experience with propeller repairs have given us the tools and know how to offer fast repair and modification services to vessels around the world. All types of operations can be carried out fast, fluently and efficiently and this afloat and underwater.
If you have any questions regarding a possible hull repair, do not hesitate to contact us. We are at your disposal 24/7 and ready to mobilize almost immediately.
+32 3 213 53 00
hydrex@hydrex.be
Click on the images below for more propeller repairs and other case studies.
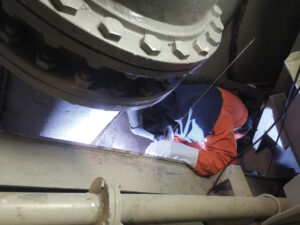
Scrubber overboard pipe repairs in Europe
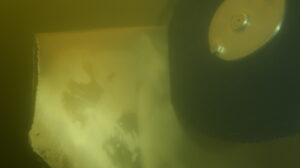
Propeller blade modifi-cations in the Netherlands, Singapore and Vietnam
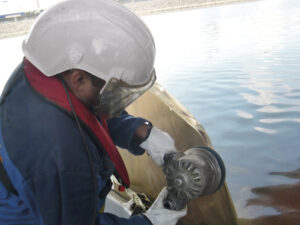
Propeller blade cropping in Ghent avoids costly drydocking
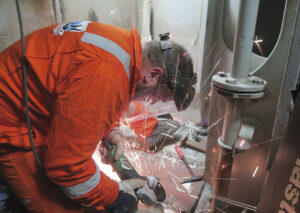
Permanent underwater insert repair on tanker in Amsterdam
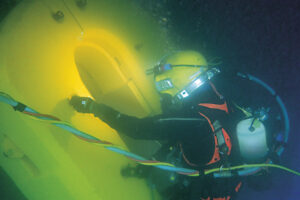
Our range of propeller repairs restore efficiency and save money
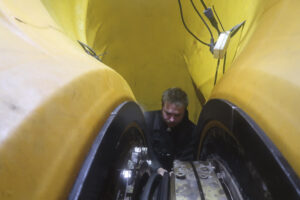