Last month our diver/technician teams carried out several repairs during one operation on a 165-meter tanker. Work on the rudder, bilge keels and bow thruster grids was performed simultaneously during the ship’s stop in Flushing, the Netherlands.
By combining these repairs into one operation we brought the needed time frame down to the absolute minimum. This allowed the owner to sail his vessel on schedule to the next stop. It is a good example of the flexibility of services we offer our customers. We adapt our work to your schedule and can easily adjust to changing circumstances.
We can also split up a repair in several stages that can be carried out in the same port during consequent visits or in different ports. This might be needed if a repair is too complex to perform during one stop or if a ship only has a very short window, as is the case with cruise ships or ferries that only make a short stopover in each port.
Our divers are trained to be flexible and to adjust to the specific circumstances of an operation.
Rudder cracks and thruster grid bolts
Our workboats are ready for immediate deployment throughout ports in Belgium and the Netherlands. This allowed us to mobilize very quickly to the ship’s location in Flushing.
Upon arrival our men split up in two teams. One team performed an underwater inspection of the bow thruster while the other technicians started working on the rudder. A previous inspection had revealed cracks on the rudder’s lower pintle area. The vessel could be trimmed enough to bring the damaged area of the rudder above water. This allowed us to access the cracks using a pontoon.
The team worked on both sides of the rudder at the same time, following the same procedure. First they used a dye penetrant test to discover the crack ends. Crack arrests where then drilled to prevent further spreading. Our diver/technicians ground out the cracks over their entire length. Next they were filled with our class approved full penetration welding.
To finalize the repair the corners of the lower pintle were re-shaped with a larger radius, as was advised by the attending class.
Meanwhile two thruster grid bolts were found missing during the inspection of the thruster tunnel. Ten other bolts had come loose. Our diver/technicians reinstalled the missing bolts and secured the other ones.
Bilge keel cropping
After reinstalling the bolts this team started the last part of the operation. The bilge keels on both port and starboard side of the ship had suffered several cracks. A total of nine sections needed to be cropped or removed underwater by our diver/technicians.
On starboard side three sections were cropped over a length of 2600 mm while one section was removed completely. On port side four sections needed to be cropped over a length between 2100 mm and 2600 mm. One section was removed completely.
Conclusion
Like all projects we undertake, we took on, organized and executed the entire job, start to finish. Throughout the operation we were in close communication with the customer, the classification society and any other party involved.
Our diver/technicians split up in two teams working simultaneously to shorten the time frame needed for the repair. This was done to make sure that any loss of time was brought down to the absolute minimum.
The owner could continue his vessel on its schedule without a costly and time-consuming trip to drydock.
If you have any questions regarding a possible on-site repair, do not hesitate to contact us. We are at your disposal 24/7 and ready to mobilize almost immediately.
+32 3 213 53 00
hydrex@hydrex.be
Click on the images below for more case studies.
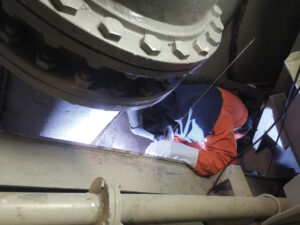
Scrubber overboard pipe repairs in Europe
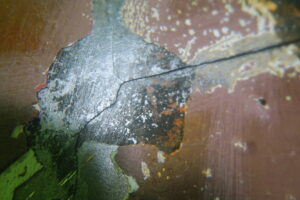
Rudder repairs in Zeebrugge, Dunkirk and Le Havre
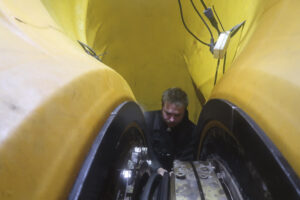
Leaking seal assembly fixed underwater in Antwerp
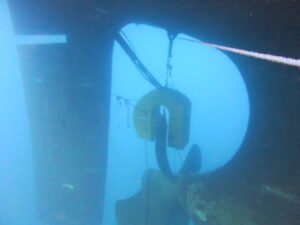
Hydrex performs propeller repairs as winter arrives

Class approved underwater shell plating replacement in Algeciras
