Our teams can mobilize immediately to perform a wide range of hull repairs on any type of vessel. In this article we give you a summary of a few operations to illustrate the diversity of shell plating repairs our diver/technicians are trained for.
Seachest insert repair in Rotterdam
A tanker suffered leakage in the starboard side seachest of its engine room. We were asked by the owner to provide an on-site solution and sent a team to the ship’s location in Rotterdam to carry out an insert repair.
On request of the class surveyor, an NDT specialist was arranged to take thickness measurements of the starboard seachest within the engine room. These measurements showed that the damage inside the seachest was wider spread than expected.
With the result of this inspection, a complete repair plan was devised in cooperation between our teamleader, the ship’s crew and the classification society.
The seachest was emptied of water and opened. All objects, including the water coolers and piping work, were removed from inside the seachest by the crew. The affected plating was then cut away. Our diver/welders worked in shifts to fit and weld the two insert plates. This was done with class approved full penetration welds.
When the installation was complete, a successful MPI test was carried out by an independent surveyor. As a result, the class representative gave his green light for the repair.
Crack repair Zeebrugge
We were contacted by the representative of a 163-meter roro vessel to carry out a crack repair during the ship’s stop in Zeebrugge. Because our fast response centers have a large stock of state-of-the-art equipment ready, mobilization for smaller operations like this can be almost immediately.
When the work area was certified gas free, our divers started the operation with an inspection of the damaged area and this on both sides of the hull. This allowed the team to take the exact measurement of the crack: 600 mm on the outside. Next a blank was installed over the area. The diver/technicians could then perform work on the crack inside the engine room without water ingress.
The team removed the frames, bulkheads and a cement box to get access to the crack. Inside the engine room it measured 700 mm. To prevent it from spreading, crack arrests were drilled at its extremities. Next our diver/technicians ground out the crack over its entire length. It was then filled with our class approved full penetration welding.
As a result of this temporary repair the owner of the vessel did not have to go off schedule for an emergency visit to drydock but could make arrangements for a follow up repair at a more convenient time and location.
Emergency grounding damage repair in Phuket, Thailand
A cruise ship suffered grounding damage while on its way to Phuket. When our technical department heard about the incident, they contacted the owners of the vessel and proposed to have our team inspect the vessel when it arrived in Phuket and perform any needed repair on-site.
Because the damage was too severe a permanent repair was not an option. A drydock visit in Singapore had therefore already been scheduled. The ship could however not sail that far on its own anymore.
First the divers performed a detailed underwater inspection of the damage. This revealed a large gap in the portside shell plating in the location of the freshwater tank. The bilge keel in this area was also severely deformed. Four smaller hull penetrations were discovered in front of the gap as well as large scraping marks and indents behind it.
After a meeting with the superintendent of the vessel and the attending class surveyor our proposed repair plan was accepted. The repair itself consisted of the installation of a doubler plate over the gap in the hull and patches over the smaller holes.
The doubler plate was designed to follow the contours of the deformed hull. Together with the patches it was fabricated by our men on-site and installed underwater. A stiffener was welded over the plate and part of the hull for extra protection. The repair was then inspected and approved by the class surveyor.
The cruise ship could sail safely to drydock in Singapore for extensive permanent repairs.
Conclusion
We have the know-how and experience needed to find the best solution for any problem you might encounter with your ships. This can be a simple routine repair or a unique complex one, as illustrated by these case studies.
All repairs are performed at the highest technical standards by our teams following in-house developed procedures. These operations are approved by the major classification societies.
Our goal is to keep you sailing with no delay.
If you have any questions regarding a possible hull repair, do not hesitate to contact us. We are at your disposal 24/7 and ready to mobilize almost immediately.
+32 3 213 53 00
hydrex@hydrex.be
Click on the images below for more hull repairs and other case studies.
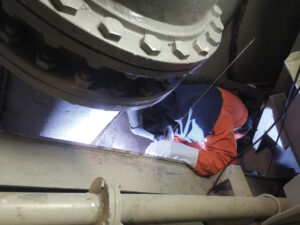
Scrubber overboard pipe repairs in Europe
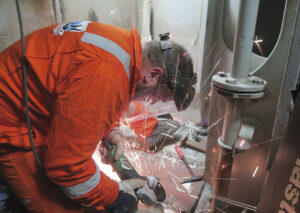
Permanent underwater insert repair on tanker in Amsterdam
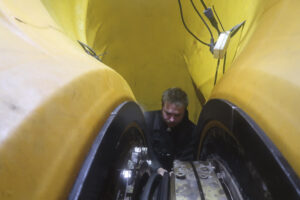
Leaking seal assembly fixed underwater in Antwerp
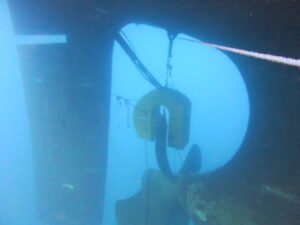
Hydrex performs propeller repairs as winter arrives
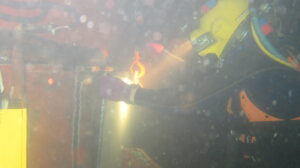
Hull repair on drill ship in Gulf of Mexico
