Rapid in-water repairs help keep the megayacht MY Savannah on charter and out of drydock.
The MY Savannah is an 84m luxury megayacht built in 2015 by Feadship, available for charter with a crew of 24 for up to twelve guests. She has the distinction of being the first hybrid superyacht and has gained numerous awards.
Depth sounder replacement
In May 2022 while waiting for the next charter to begin, a situation arose which needed immediate handling. The Savannah’s captain, Chris Durham explains, “We had a situation whereby in the space of seven days we encountered quite severe issues with both depth sounders – for redundancy we have one forward and one aft. The aft one stopped transmitting completely and the forward one became very intermittent and didn’t give us a solid echo. It was quite a tricky situation,” adds Chris. “You’re not allowed to sail without depth readings and it’s certainly not something you want to be without if you’re navigating anywhere.”
The Savannah’s engineers found that the transducers could not be replaced from inside the yacht.
“Time was incredibly important to us…”
“When they told me that we couldn’t repair the depth sounders without coming out of the water, I started to look a little further into why, and what we could do to fix that,” says Chris. He reached out to the technical advisor at their management company, Y.CO Luxury Yacht Management. “They gave us contact information for two companies who might help, one of which was Hydrex,” Chris recalls.
“When I went to the Hydrex website and saw that changing transducers was a specific service offered, I got on the phone right away. I had a really good conversation with a very knowledgeable young man at Hydrex. “
“Time was incredibly important to us as we didn’t know the exact schedule of the upcoming charter, so we were very impressed with what we were able to accomplish and organize over a weekend,” Chris continues. “Having initially reached out on Saturday, by Sunday we had arranged for a team to fly out on Tuesday, complete the job on Wednesday and fly back on Thursday. It was extremely swift correspondence late into the night on the weekend, and very helpful – solutions not problems.”
The Savannah was in Göcek, Turkey at the time. Chris was not familiar with the local yards and his alternative would have been to go to drydock in Genoa or Barcelona. “A rough estimate of the cost of going to drydock was an absolute minimum of 25-30,000 euro just for us to come out of the water to do the repair. As soon as it reached two, three, four or five days it would have been a lot more. And that was without taking into account the cost of getting there and back.”
The job itself went exactly according to plan. Chris says, “It was a professional experience from the get-go: from the initial correspondence to stepping on board to the post report, it was a really seamless, smooth operation. The Hydrex team arrived on time or ahead of time, a well-presented, fit, strong team,” Chris recalls. “We went over the plan and which depth sounder we were going to tackle first and we set to work. The actual work went very well. The Chief Engineer was very happy with how everything developed and progressed.
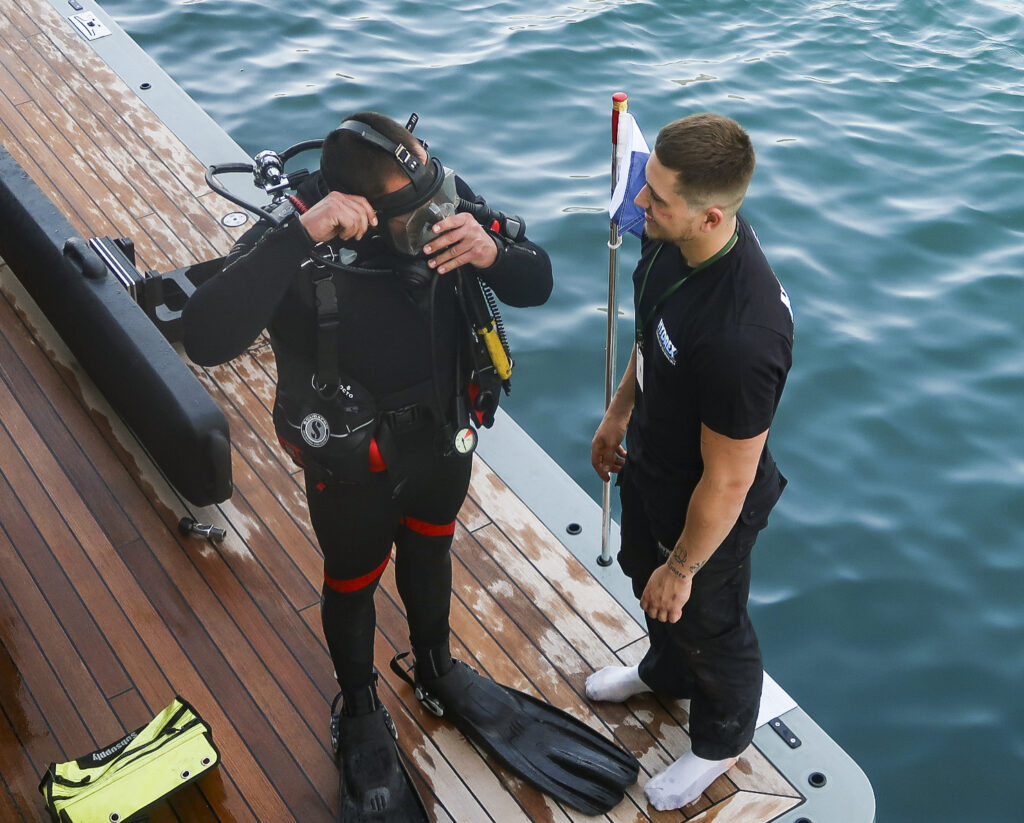
We were able to successfully switch out the forward and the aft transducers and it was done safely. There was certainly a high awareness and focus on safety which is very much how we like to operate, with signage and risk assessments and procedures from the vessel side and from Hydrex. I was very happy to see a very thorough mindset for safety there.”
The total cost of the job was less than half of what it would have been if the Savannah had had to go to drydock.
Anode replacement
Following the success of the transducer replacements, the Chief Engineer, Andrew Gerrard, decided a few months later, when the Savannah was in Antibes, to contact Hydrex and use the same approach for another problem that had been nagging and which had looked like it could only be remedied in drydock.
Andy explains, “Our main sea strainers were becoming fouled very quickly and as a result the frequency of manual cleaning required had greatly increased. We were already experiencing an increase in temperatures in our LT and HT cooling systems and the coolers required manual cleaning on a monthly rather than 6-monthly basis. This would have only increased with the amount of time ‘unprotected,’ eventually to a point where we couldn’t have kept up with the manual cleaning and it would have stopped us from sailing.”
“We were pleased with the results of the transducer job, so decided to do the anode replacement on the same basis,” says Andy. “Our contact at Hydrex was very thorough and quick to reply. I felt as though we were in safe hands from the get-go. The team mobilized very quickly which worked very well with our busy schedule.”
“We aren’t often in the same place for very long so it was important to be able to undertake the job without a big time window. They really fitted around us and our schedule and were very willing to help out with all aspects of the anode replacement. The job was completed to our full satisfaction. The anodes are now fully functional and leak-free and it has prevented us from having to drydock the vessel outside our normal schedule. We are very pleased with the resolution.”
Summing up
The Savannah’s captain concluded, “The biggest thing with these jobs, even though they were not overly complex for your team in comparison to some of the work they do, was peace of mind for us. The work has to be done correctly. Having that expertise and competence on board with the Hydrex team who can fix something if it doesn’t quite go to plan or any issues come up with changing an anode or a transducer in the water was probably the biggest thing for us.”
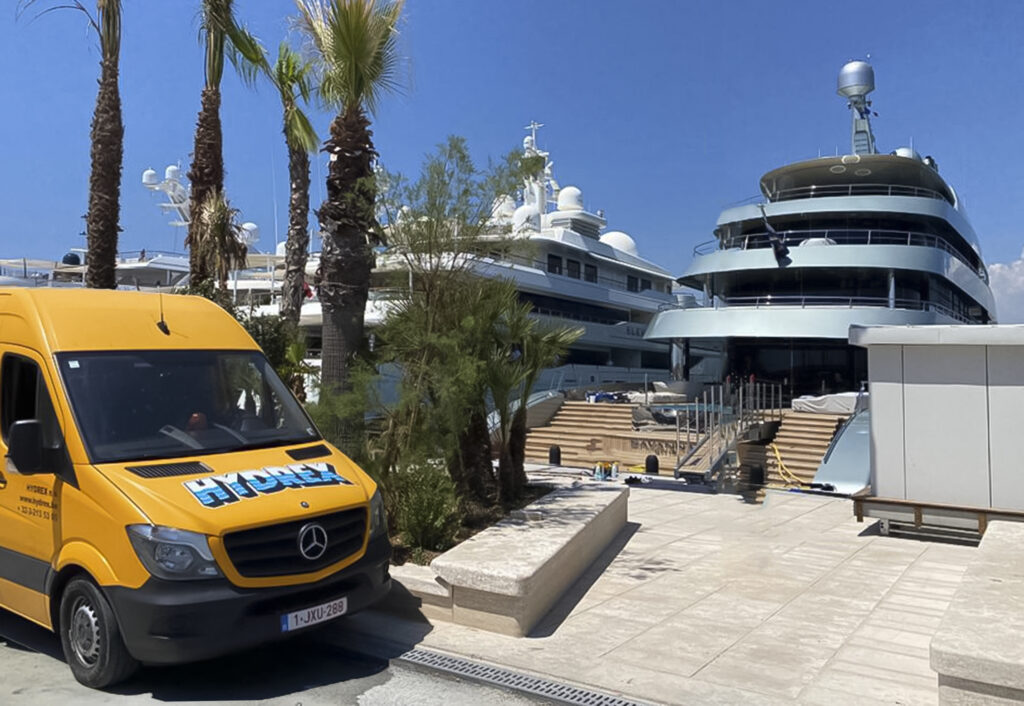
He reiterates his first impression of Hydrex: “You usually have to wait for people to reply and so on. Being able to organize the job so quickly over a weekend, I was like, ‘Wow, OK! This company is obviously well organized, well managed, well run, eager for work.’ Brilliant!”
This was business as usual for Hydrex and a perfect example of providing fast underwater and afloat service to vessels in need, so as to keep them in service and out of drydock. Whether it’s a 350 meter container ship or cruise ship, or an 84 meter super yacht, the same expertise and level of service is available to provide a rapid, high quality solution.
If ever you need assistance with the underwater part of your vessel, give us a call. We can then tell you if the repair is feasible and start working on its handling.
+32 3 213 53 00
hydrex@hydrex.be
Click on the images below for more case studies.
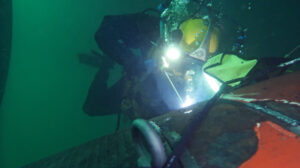
Underwater stern tube seal replacement avoids drydock
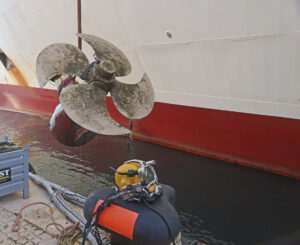
Underwater bow thruster removal and reinstallation in Naples
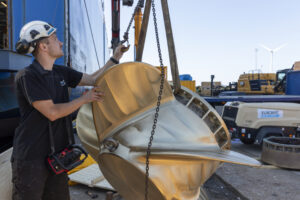
Start saving fuel with your propeller cone fin now
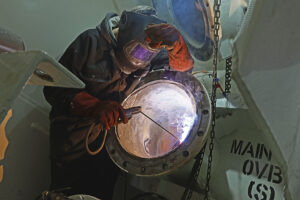
Scrubber overboard pipe operations on sister vessels in Denmark
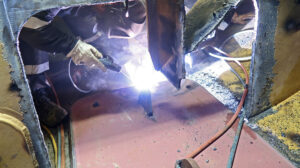
Permanent underwater insert repair on bulker in France
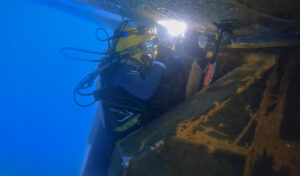